PLANIFICACIÓN Y PROGRAMACIÓN: SIEMPRE SE CREE QUE
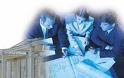
Por Erol I. Zabiski Duardo
EL PROCESO DE PLANIFICACIÓN Y PROGRAMACIÓN DEL MANTENIMIENTO. DEFINICIÓN DEL QUÉ HACER, CÓMO HACERLO Y CON QUÉ (Fragmentos)
Dentro de los procesos de Gestión de la Función Mantenimiento, existe uno que llama la atención de todos los mantenedores, por la contradictoria relación que se plantea entre dos características fundamentales: DINÁMICA y RIGIDEZ. La primera está enfocada a la necesidad de establecer planes de Mantenimiento, donde se prevé la ejecución de acciones de Mantenimiento para evitar la falla de los equipos, pero que está condicionada al comportamiento real dentro de las líneas de producción y/o servicio. La segunda característica, la obtenemos según la obstinada razón de planificar y no corregir los elementos ni en función del tiempo ni en función de las acciones. Esta contraposición, sugiere una revisión constante de los programas de Mantenimiento, y de las tareas o acciones que se pretenden acometer. Si partimos de la base de establecer la Planificación, como un proceso, dinámico, complejo y estratégico, podemos entender que estamos frente a un problema de muchas variables y que es necesario su estricto control. Partiremos de la definición conceptual de los procesos, para entender mejor este criterio. Según el Sr. Thomas H. Davenport, en su libro “Process Innovation: Reengineering Work Through Information Technology”, plantea que los procesos de Gestión típicos de cualquier organización pueden ser establecidos como:
1. Gestión del desempeño.
2. Gestión Información.
3. Gestión de Activos. (Mantenimiento).
4. Gestión de Recursos Humanos.
5. Planificación y Organización (Distribución de recursos.)
Etos procesos, que incluyen los de Planificación, son definidos para una empresa en su totalidad, pero aparecen dentro de los que la Gestión del Mantenimiento establece. Por esto, podemos definir como Procesos al ““…conjunto de actividades mutuamente relacionadas o que interactúan, las cuales transforman elementos de entrada en resultados” Si bien es cierto que la característica fundamental de la Planificación es la “relación entre actividades”, es también, la “transformación de elementos de entradas en resultados”, criterio que favorece la calificación de la Planificación del Mantenimiento, como el “PROCESO DE PLANIFICACIÓN”.
Verdades” del Proceso de Planificación.
Enla Nota Técnica titulada “Tres creídas Falsedades”, del MSc. Ing. Luís F. Sexto, se exponen algunas falsedades que se resumen a continuación:
FALSEDAD #1: El Mantenimiento ya no es un conjunto de actividades que permiten que los equipos se mantengan funcionando, si no que permiten que no falle la función Objetivo para el cual fue diseñado, montado y está operando. Este criterio, es el punto de partida para ejecutar un Proceso de Planificación coherente, dinámico y que facilite el cumplimiento de los objetivos propuestos.
FALSEDAD #2 Si ejecutamos acciones de Mantenimiento que garanticen mantener la Función Objetivo, entonces todas aquellas acciones previstas que no garantizan esto, deben ser revisadas, eliminadas o rediseñadas, comparando costo de ejecución, vs. costos de indisponibilidad, suponiendo que ocurriera la falla. Esta comparación de costos, que puede ser considerada como elemento Vital, será analizada en otro contexto, fundamentalmente por su nivel de importancia y riesgo, si no es tomado en cuenta.
FALSEDAD #3: El Indicador Tiempo Medio Entre Falla (TMEF) es el mejor elemento de juicio que existe para planificar (define frecuencia de intervención), sobre todo porque implica un tiempo probable de trabajo libre de fallas, pero que establece una probabilidad de ocurrencia de un 37%, si partimos de dos suposiciones: que se trabajaron con valor confiable y que estamos en la etapa de la vida útil del equipo, o sea, tasa de falla constante. Difícil ¿no? Entonces, a partir de aquí se establecen otras falsedades que están relacionadas con el trabajo según datos Históricos, para lograr frecuencias de programación, o vincular estos “históricos” con un chequeo de la Condición Real de los equipos. Además, establecer la herramientas y técnicas de trabajos que más se adapten al contexto operacional imperante, para así obtener información vs. la utilización de cualquier método o herramienta, sea esta necesaria o no, o simplemente, porque “…dieron resultados positivos en la empresa X …”. Estos errores, son comúnmente cometidos en la mayoría de las instalaciones, pero pueden ser eliminados, si hacemos análisis económicos, acompañados de los análisis técnicos, para definir la factibilidad de la herramienta o método de trabajo a incorporar. Este ultimo elemento, podemos definirlo como la falsedad #7, encontrada dentro del Proceso de Planificación, y que afecta el posible resultado a alcanzar. Si alguien me preguntara cual es la mayor verdad dentro del Proceso de Planificación, sin pensarlo mucho respondería “que no existe ninguna verdad demostrada.” Por eso, enfocaremos esta definición del QUÉ HACER, CÓMO HACERLO y CON QUÉ, a partir de la definición de la Función Objetivo a mantener, y los Objetivos Productivos o de Servicios de la Empresa en cuestión. Esto es lo más cercano a la verdad, pues siempre va a depender de determinados contextos operacionales o de servicio.
Definición de …
Para comprender los elementos internos a desarrollar dentro del Sub.-proceso de Planificación, es necesario responderse algunas preguntas interesantes, relacionadas con la Planificación de Acciones y Recursos, de cuyas respuestas se obtendrán todos los pasos de la Planificación, y el cumplimiento de los objetivos propuestos. El punto de partida será responder:
v ¿DÓNDE EJECUTAR LA ACCIÓN? La definición de DÓNDE EJECUTAR la acción de Mantenimiento, estará condicionada a la identificación del equipo/sistema/instalación, que debe mantener una función vital dentro del proceso. Se define “función vital” a partir de criterios ya establecidos por el RCM, y que pueden ser de Seguridad Operacional, Afectación directa o indirecta al Medio Ambiente, o Riesgos de accidentes para la Vida Humana. Estos criterios, pueden ser obtenidos con el desarrollo de esta técnica (Mantenimiento Centrado en la Confiabilidad) pero es considerado un error esperar su incorporación para poder decidir con exactitud, cuáles son los equipos fundamentales a incorporar dentro del Programa de Mantenimiento, evitando su falla.
v ¿QUÉ ACCIÓN EJECUTAR? La acciones a ejecutar serán el resultado de un análisis, que permita establecer las posibles fallas, y las acciones que se pueden acometer para evitarlas. Si partimos que los equipos/sistemas pueden fallar por muchos motivos, entonces entenderemos que este estudio no es nada sencillo, pero no ejecutarlo incorporaría acciones al Plan de Mantenimiento, que no implican seguridad del proceso y sí muchos fallos y gastos de dinero y pérdidas de disponibilidad. Uno de los resultados fundamentales de este estudio, es obtener acciones de Mantenimiento, pensadas y diseñadas para atacar tres aspectos críticos: acciones que restablecen el nivel de desempeño del equipo; acciones que atacan directamente el defecto que provoca la falla; y acciones que atacan la causa-raíz del problema y que implica no incurrir en fallas crónicas, afectando someramente la calidad del servicio o producción previstos. Aquí, se recomienda hacer un Análisis de PARETO, para establecer, según un histórico de datos, las fallas comunes de los equipos/sistemas, su impacto tanto económico como productivo, y atacarlas con acciones bien diseñadas, unido al establecimiento de prácticas de Mantenimiento Predictivo para hacer el seguimiento necesario, según el tipo de equipo y/o sistema. Es inmensa la complejidad encontrada en el análisis de las acciones según las necesidades; pero técnicas como el Análisis de Causa Raíz, el RCM, el estudio de fallas con grupo de Expertos, el estudio de Históricos y las normativas y/o recomendaciones del fabricante, pueden ser consideradas dentro del proceso, y paulatinamente ir mejorando las acciones, su diseño y su ejecución. Obtenido el par OBJETO-ACCIÓN (que representa más del 60% del sub.-proceso de Planificación), podemos establecer otros puntos importantes. La siguiente pregunta a responder, está relacionada con los recursos que intervienen.
v ¿CON QUÉ EJECUTARLA? Definir con qué ejecutar alguna acción de Mantenimiento, estudiada, analizada y prevista por su impacto positivo en el cumplimiento de los objetivos, se divide en tres (3) criterios fundamentales: RECURSOS HUMANOS, RECURSOS MATERIALES y RECURSOS FINANCIEROS. Como la conformación del Programa de Mantenimiento, lo ejecutan y conforman muchos factores internos de la organización, aunque es considerado algo puntual comparado con la ejecución, es muy importante saber cuales son, -y UD. desea que sean- las Competencias Laborales del personal que interviene en toda la conformación, desde la preparación hasta la ejecución de las acciones previstas. En este aspecto, debemos diferenciar las Competencias Laborales del Grupo de Planificación y Control y las de los Ejecutores. Ls Competencias Laborales del Grupo de Planificación y Control son: Capacidad de Toma de Decisiones basada en multi-criterios, Amplio conocimiento técnico de las máquinas, equipo/sistemas a planificar, Conocimientos económicos que permitan ver variantes de acciones a planificar, Conocimiento exactos de las condiciones del taller de construcción, suministro de piezas de repuesto y aspectos legales de contratación de servicios a terceros, Priorización de acciones de Mantenimiento, en función de las condiciones establecidas o posibles a establecer en el periodo a planificar, etc. Para el Personal que ejecutará las acciones de Mantenimiento se establecen criterios de selección y/o competencias laborales, que están enmarcadas en: Requisitos y responsabilidades, Contenido del Puesto de Trabajo, Condiciones del Puesto de Trabajo (Herramientas y/o instrumentos) y Conocimiento técnicos necesarios para ejecutar las acciones. Estos últimos, estarán ajustados a las especialidades de Electricista, Mecánico, Instrumentista, Especialistas del Grupo de Inspección y Diagnóstico, Energético, Refrigeración, climatización, Lubricación y engrase, Acumuladores, entre otras, todas necesarias dentro de las condiciones de la empresa/industria en cuestión. La definición de las empresas a contratar, es un asunto tan delicado, que es preferible que cada cual establezca los criterios, según su contexto operacional y su entorno empresarial, para evitar malas interpretaciones. E el caso de los Recursos Materiales y Financieros, los elementos a tener en cuenta varían desde los necesarios según las tareas acometidas, hasta las técnicas de cálculo de presupuesto, aspectos legales y ciclo de logística establecido en la empresa. Pero ¡cuidado! Siempre hay que pensar primero en el “Cumplimiento de los Objetivos estratégicos trazados”. Sin esta referencia, no es posible hacer nada.
v ¿CÓMO EJECUTAR LAS ACCIONES? Increíblemente, siempre se piensa que saber los pasos necesarios, es simplemente establecer “Procedimientos” de trabajo, o seguir “Normativas” ya establecidas. Aunque esto no está muy lejos de la verdad, es menester cuidar que tanto los ejecutores de las acciones, como las empresas contratadas, sigan las Normas de Seguridad propias de la instalación, así como los procedimiento que se previeron, puesto que cada empresa tiene su características, y no es posible extrapolar criterios de una hacia otra, sin cometer errores, ni causar daños ulteriores. Por esto, se recomienda analizar como ultimo criterio las normas a seguir, explicarlas a todos los miembros del Staff de Mantenimiento, y hacer revisiones anuales de ellas, sobre todo, por los cambios que puedan existir en las condiciones de los equipos/sistemas, y las variaciones en las acciones. No se puede perder de vista que aunque todos los pasos necesarios para el cumplimiento del programa de Mantenimiento sean previstos, si no se ejecutan al pie de la letra, es como si nada de lo anterior existiese. Las personas son el eslabón fundamental dentro de los errores que se puedan cometer.
2 comentarios
FLORENCIA -
en verdad muy buen material.gracias por este aporte.
cordialmente florencia.
Enrique Gabriel -
Saludos, Gabriel.