INTRODUCCIÓN Y APLICACIÓN DEL PRINCIPO DE PARETO
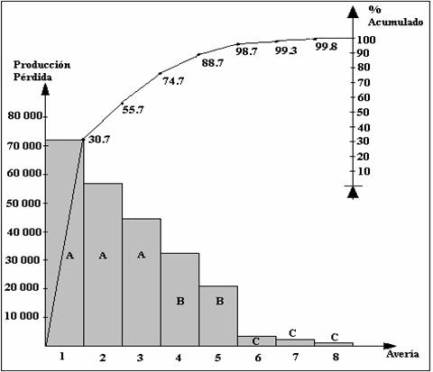
Por Luis Felipe Sexto
El principio de Pareto (realmente formulado por Joseph M. Juran en 1937, ver también ¿¡FIN DEL PRINCIPIO DE PARETO!? ) constituye un método de análisis que permite clasificar y jerarquizar cualquier problema del tipo que sea. Un diagrama debidamente construido pone en evidencia la dirección hacia donde deben concentrarse los esfuerzos, para disminuir o eliminar los aspectos del problema que más inciden en la situación que se estudia. Es muy factible la utilización de los diagramas de pareto cuando se pretende dirigir la atención de un modo sistemático a los problemas, específicamente cuando se dispone de medios limitados para resolver una gran cantidad de los mismos. El principio es muy útil para dar prioridad a aquello con lo que se debe trabajar primeramente. La técnica tiene su base en aquello de lo poco vital y lo mucho trivial, que se cumple en muchos aspectos de la vida. El principio tal y como se enuncia dice “En cualquier negocio o industria pocos elementos son vitales mientras que la gran mayoría no lo son “. En general significa que entre una serie de objetos, equipos piezas, personal, etc., aproximadamente el 20 % de los elementos representan el 80 % de los problemas o desviaciones. De aquí que dichos objetos o elementos se clasifiquen como se indica a continuación.
La técnica de pareto consta de tres pasos fundamentales que a continuación se relacionan:
1. Paso 1-. Se define qué aspectos se incluirán en el diagrama, el título, el período que se está analizando (fecha desde–hasta), las unidades en que se expresan las magnitudes y el origen de los datos.
2. Paso 2-. Consiste en realizar la tabla estadística a partir de las sumas totales de magnitudes observadas o registradas tal y como representan los diagramas que se muestran luego de esta explicación. Este paso también incluye la confección de la tabla resumen por clase.
3. Paso 3-. Es la construcción y el análisis del diagrama de Pareto como tal, basado en lo registrado por la tabla estadística y la de resultados. Incluye la elaboración de un plan de mejoras dirigido a los elementos designados como clase A.
Tabla 1. Tabla de datos para construir el diagrama.
Análisis anual de las pérdidas en la producción a consecuencias de averíasen máquinas críticas de la fábrica de helados “G”. | |||||||
Avería | Valor de la producción que no se realizó (U$D) | Acumuladopor rubro | åi | å% | Clasificación por clase | ||
1 | Cambio de rodamiento. | 70830 | 30.7% | 70830 | 30.7 | A | |
2 | Cambio de correas. | 57057 | 25% | 127887 | 55.7 | A | |
3 | Problemas con los sellos del Homogenizador. | 43285 | 19% | 171172 | 74.7 | A | |
4 | Problemas con la bomba de gas-oil | 31479 | 14% | 202651 | 88.7 | B | |
5 | Problemas con la empaquetadura de la bomba de agua de la caldera | 23610 | 10% | 226261 | 98.7 | B | |
6 | Fallos de una transmisión homocinética en la maquina de paleticas | 1418 | 0.6% | 227679 | 99.3 | C | |
7 | Problemas con los cilindros de alta y baja presión en le maquina de paleticas. | 1134 | 0.5% | 228813 | 99.8 | C | |
8 | Deficiencia en el funcionamiento de la máquina de paleticas debido al desgaste de la cadena | 567 | 0.2% | 229380 | 100 | C | |
TOTAL | 229380 | 100% | |||||
Tabla 2. Resultados del análisis de PARETO, fábrica de helados “G”.
Resultados de la fábrica de helados “G” | |||
CLASE | % de elementos dentro de cada clase | % acumulado que representa cada clase | Razón de importancia por clase |
A | 37.5 | 74.7 | 1.99 |
B | 25 | 24 | 0.96 |
C | 37.5 | 1.3 | 0.03 |
El 37,5% de las averías representan el 74,7% de las pérdidas de producción. La información tabulada se representa en el diagrama que muestra la figura del inizio del artículo. Es necesario aclarar que las ocho averías que se tomaron en cuenta no son las únicas. Sucede que en la fabrica “G” no se registran el 100 % de las averías, sino sólo las que afectaron más severamente a la producción. Por lo que la técnica de Pareto se acerca a la realidad pero no a toda la realidad. Según los resultados de “G”, las averías que provocaron un daño mayor en la producción (del año 1997) están referidas a fallas de los rodamientos, fallos de correas de las distintas máquinas críticas y a problemas con los sellos del homogeneizador. En consecuencia se dejaron de producir, sólo por ellas, valores equivalentes a un aproximado de $171 172, según los resultados del análisis.
0 comentarios