¿Qué es RCM? Una interpretación de la línea guía SAE JA 1011
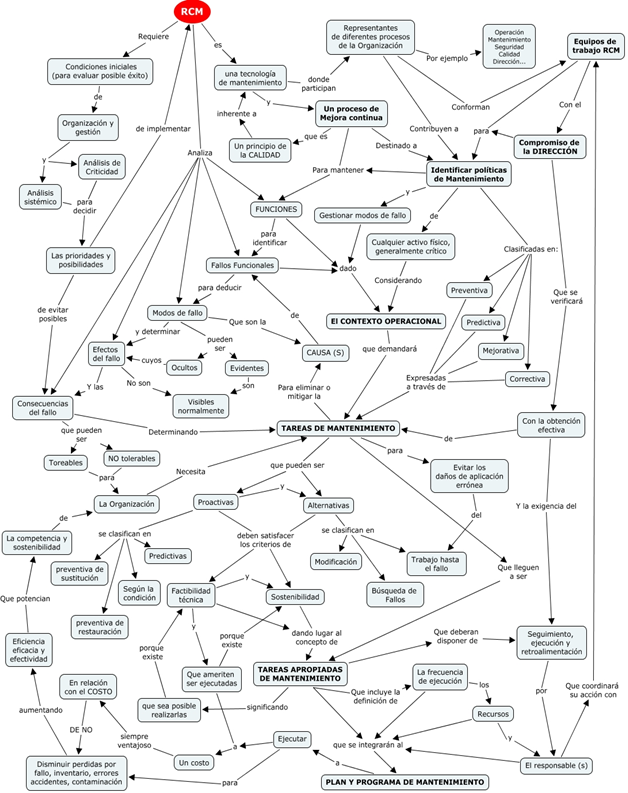
Mapa Conceptual del proceso RCM (Reliability Centered Maintenance). Luis Felipe Sexto, ©2007 Creado con IHMC Cmap Tools
Mapa Conceptual del proceso RCM (Reliability Centered Maintenance). Luis Felipe Sexto, ©2007 Creado con IHMC Cmap Tools
Por Luis Felipe Sexto
Puede suceder que una máquina (sistema, proceso, línea) se encuentren en inactividad por cualquier razón de tipo operativa o logística y se decida aprovechar esa ventana que se abre generosa en el proceso productivo para realizar algunas acciones de mantenimiento. Por ejemplo, como sugirió una lectora de este espacio, tenemos el caso de una fresadora, que se detiene por la necesidad de realizarle una corrección al husillo y se aprovecha la parada para limpiarla, chequear los mandos, verificar la integridad, cambiar o rellenar el aceite del reductor.... Seguramente que por instinto, muchos de nosotros aprovechamos las paradas ocasionales y ejecutamos actividades paralelas que pudieran no estar relacionadas en primera instancia con la causa de dichas paradas.
En concreto, las intervenciones que se pueden clasificar como de Mantenimiento de Oportunidad, son aquellas que hay que hacer, pero que pueden esperar a una próxima parada sea por mantenimiento programado, o por averías, o por ventanas que se abren durante la operación por diversas razones relacionadas con esta. En otras palabras, las acciones de oportunidad son necesarias pero no críticas y por ende su prioridad es baja por definición.
Es importante reconocer que a lo que se llama "Mantenimiento de Oportunidad" no es un nuevo tipo de política de mantenimiento, sino que es una acción que puede estar planificada pero su programación esta caracterizada por la posibilidad de ser ejecutada según las "oportunidades" de tiempo y mano de obra. Muchas de estas acciones de oportunidad pueden ser ejecutadas por el operario mismo, sin tener que llamar al personal especializado de mantenimiento. Lo único que para ello, el operario debería tener la lista de esas intervenciones necesarias, el acceso a eventuales materiales o herramientras a utilizar y, naturalmente, la autoridad y conocimientos necesarios. Todo ello con el objetivo de no programar más tiempo de parada para ejecutar dichas acciones que se encuentran en un estado de "hibernación".
Se trata, en suma, de acciones de mantenimiento con alto nivel de flexibilidad que siempre es aconsejable tener identificadas para aprovechar eficaz y eficientemente las paradas operativas sean indeseadas o no, e intentar así disminuir los tiempos de mantenimiento planificado, al realizar sólo aquellas actividades que requieren la parada verdaderamente programada según el plan o debido a una fuerza mayor. ◙
Por Luis Felipe Sexto
Por Luis Felipe Sexto
Es conocido, cuan maltrecho queda el concepto de Mantenimiento Productivo Total, cuando se le pretende reducir a sólo uno de sus pilares. La evidencia apunta a desestimular la idea de una implementación robusta y definitiva del TPM, toda vez que, hacerlo seriamente, significa quizás cambiar la estructura organizativa, el modo de gestionar y los estilos de dirección en nuestra empresa. Esto más que un estimulo, representa una franca amenaza a la posición y al orden tradicional de hacer las cosas.
La gran contradicción viene dada por el hecho que un grupo importante de dirigentes empresariales desean y declaran la necesidad de mejorar e incrementar la productividad y obtener resultados sin precedentes… siempre y cuando no cambien mucho las cosas. Sin embargo, al menos se necesita hacer referencia a una metodología con alta apariencia innovadora y con resultados demostrados en otras organizaciones, para validar las intenciones previamente declaradas ante un consejo de dirección (por ejemplo). Apliquemos el TPM siempre que el TPM no se aplique esencialmente, parece ser el mecanismo actuante.
¿Que entendemos por aplicación esencial del TPM? En este punto tendríamos que decir, que al menos se necesita satisfacer los siguientes cuatro puntos:
1. Constancia de propósito.
2. Implementación evolutiva y planificada.
3. Dominio y aplicación de TODOS los pilares.
4. Participación de TODAS las áreas y de TODO el personal de la empresa en la implementación.
Estos cuatro aspectos parecen críticos y absolutos, ya que no es posible llegar a resultados meritorios o esperados si no se satisface cada uno de ellos. Hay un detalle que parece inofensivo pero que apenas se pretende la implementación comienzan las sospechas de que será muy complejo llegar al final. El detalle es el requisito de participación de todo el personal y de todas las áreas.
Aquí la contradicción viene relacionada con las estructuras verticales, fragmentadas y poco participativas que presentan un gran número de empresas. ¿Cómo hacer participar a todos si mi estructura organizativa es esencialmente contraria a la participación? ¿Cómo lograr la participación entusiasta de la gente en el mantenimiento autónomo si están habituados y condicionados a mantenerse en posición pasiva y esperar órdenes de los mandos, porque allí, la motivación, las iniciativas y el sentido de pertenencia no se consideran aspectos relevantes a inculcar?
Si la iniciativa es seria, entonces hay que revisar la estructura y la preparación y disposición al cambio de la dirección. De otra parte, sin constancia de propósito esta asegurado que no se llegara a ninguna parte. Por ello, después de un tiempo los directivos que no poseen esta visión inician a pensar en introducir otra metodología ya que el TPM “no ha dado los resultados esperados” y de consecuencia “estamos pensando en implementar”… otra cosa. Esa otra cosa la podemos dejar a la imaginación del lector.
Se puede hacer una lista grande de posibles esperanzas inútiles de sustitución del TPM. La raíz del asunto es que no se concibe el cambio estructural, organizativo y de dirección que sería coherente con la pretensión de implementar un sistema de gestión como el TPM que impacta transversalmente en toda la empresa. Se recurre entonces a las tecnologías menos agresivas al status quo o que actúan solo a nivel localizado, pero que igualmente, por las mismas razones, no dan los resultados esperados y así se continúa creando esperanzas con técnicas, metodologías o etiquetas de moda. La moda siempre regresa disfrazada.
El aspecto más degradante e irrespetuoso que ha tenido que sufrir el TPM esta relacionado con sus pilares. El hecho de pretender hacer pasar “gato por liebre”. Es decir, afirmar, asegurar y hasta jurar, que la fórmula Mantenimiento Autónomo es igual a TPM, es correcta. O peor aún ¡¡¡que 5S=TPM!!! Es este quizás la incoherencia mayor a la ética y naturaleza sistémica que esta a la raíz y la practica del TPM.
A todo esto bastaría una pregunta: hey, alta dirección! ¿Qué dicen ustedes del resto de los pilares, cómo y cuando los piensan implementar? ¿Se puede creer seriamente que haciendo un tentativo de introducir el Mantenimiento Autónomo aisladamente y forzando la estructura verticalista se pueden obtener los resultados potenciales del Mantenimiento Autónomo? ¿Y los demás pilares no hacen falta? ¿Para qué están? ¿Será que no tienen sentido o que no cuadran con el modo que funciona la empresa? El TPM es un sistema articulado y coherente, si le faltan pedazos ya no será más TPM. No sabemos que será, pero al menos podemos saber lo que no es.
El TPM nació como un modo de entender la empresa en su conjunto y no como una metodología a la que se le puede violentar a que trabaje en un encuadramiento incompatible con sus principios. El TPM no se adapta a nuestra estructura, el TPM requiere e impone un tipo de estructura que si no coincide con la nuestra, y tampoco estamos dispuestos a cambiarla, todavía menos podremos aspirar a los resultados y potencialidades de lo que es capaz.
Por ello, El JIMP ha desarrollado los premios y los criterios de elegibilidad de los mismos. De ese modo es posible premiar la coherencia y la constancia, y sobre todo, los resultados que se pueden esperar por ser demostrados en la práctica de muchas empresas en casi todos los confines del mundo durante décadas.
La elegibilidad, para aspirar a uno de los premios TPM del JIMP, queda determinada como sigue:
1) El Premio a la Excelencia en TPM, Categoría B:
· Debe tener aproximadamente 2 años de actividad de progreso después de la introducción del TPM.
· Debe haber desplegado la actividad basada en 5 pilares del TPM y centrada en el lugar de producción (mejoras individuales; mantenimiento autónomo; mantenimiento planificado; educación y desarrollo; seguridad, saneamiento y el control ambiental).
· Debe haber completado el paso 4 para la actividad de mantenimiento autónomo.
· Debe haber completado el desarrollo de la infraestructura para la actividad del TPM, con resultados tanto tangibles como intangibles.
2) Premio a la Excelencia en TPM, Categoría A:
· Debe tener aproximadamente 3 años de realización después de la introducción del TPM.
· Debe haber desplegado la actividad basada en 8 pilares de TPM, por todos los miembros del personal de planta (mejoras individuales; mantenimiento autónomo, mantenimiento planificado; Gestión inicial; mantenimiento de calidad; administración y supervisión; educación y desarrollo; seguridad, saneamiento y control ambiental).
· Debe haber completado el paso 4 para la actividad de mantenimiento autónomo .
· Debe haber completado el desarrollo de la infraestructura para la actividad del TPM, con resultados tanto tangibles como intangibles.
3) Premio a la Excelencia en el compromiso consistente con el TPM:
· Debe haber recibido el Premio a la Excelencia en TPM (categoría A o B).
· Debe tener aproximadamente 2 años de actividad de progreso después de recibir el Premio a la Excelencia en TPM (categoría A o B).
· Debe estar desplegado la actividad basada en los 8 pilares de TPM, por todos los miembros del personal de planta.
Para referenciar este documento:
Electronic Document: Sexto, Luis Felipe. ¿SU EMPRESA PUEDE ASPIRAR A UN PREMIO TPM? [en línea]. Marzo de 2009. [fecha que se cita xx/xx/20xx]. Disponible en Internet: blog Calidad & Mantenimiento <http://luisfelipesexto.blogia.com> .
Se permite la reproducción de este documento, siempre que se referencie la fuente y no exista ánimo de lucro.
La ISO 9001:2008 no introduce nuevos requisitos sino que establece clarificaciones a la versión del año 2000, y aumenta su compatibilidad con la norma ISO 14001:2004 de Gestión Ambiental. No obstante cada Organización deberá evaluar las mejoras a introducir para adaptarse a la nueva norma.
Por Luis Felipe Sexto
EN MUCHAS OCASIONES no se advierte limpiamente por qué si la organización tiene un aparente buen nivel de producción y ventas, su situación con las deudas y con las inversiones se torna compleja...
Siga leyendo desde el Portal Latinoamericano de Mantenimento (www.mantenimientomundial.com)
Por Luis Felipe Sexto
Normalmente es conocido que el Análisis de Modos de Fallos y Efectos (en inglés Failure Mode and Effects Analysis, FMEA) es uno de los instrumentos más importantes en los estudios de confiabilidad. Se utiliza principalmente en las fases iniciales del diseño de un sistema, sin limitarse a ella ya que es sumamente útil aprovecharlo también durante la fase operativa, con el objetivo de identificar los diferentes modos de fallos posibles y poder actuar efectivamente sobre los efectos indeseados. Si al análisis FMEA se le agrega un modo para determinar prioridades, siguiendo ciertos criterios, nace la lista de elementos o modos de fallos criticos y con esto lo que se conoce como FMECA (Failure Mode, Effects, and Criticality Analysis).
Hata aquí, seguramente que no hay nada novedoso y es lo que más o menos conocemos convencionalmente. Sin embargo, creo merece la pena comentar la existencia de una versión desarrollada en Italia que dicen se trata de un FMECA, y en efecto se conoce como MAGEC, que en esa lengua significa Modi e Analisi dei Guasti, degli Effetti e delle loro Criticità, es decir FMECA en italiano… pero las apariencias, apariencias son, parece pero no es un FMECA.
¿De que se trata entonces? En esencia se base en el FMECA, pero claramente se aplica durante la fase de operación del sistema objeto de análisis al fin de establecer un plan de mantenimiento; exige la descomposición del sistema generalmente hasta el nivel de componentes críticos (subsistemas, unidades funcionales, componentes críticos). Luego realiza el análisis de los posibles modos de fallos (aquellos que han sucedido y los que pueden suceder dado el contexto), y describe los efectos. Hasta aquí no hay nada nuevo. Luego se aleja del proceso convencional FMECA y continua una línea interesante para llegar a establecer un plan de mantenimiento estructurado.
La primera divergencia es que concibe la proposición de una serie de tareas de mejoramiento a continuación del análisis de la criticidad de los fallos. Estas tareas de mejoramiento son derivadas del análisis de los efectos de los modos de fallos y de los defectos o puntos débiles del diseño del sistema que se detectan. Luego el MAGEC pasa a la proposición de las tareas de mantenimiento y de automantenimiento (mantenimiento autónomo). Este último es la respuesta del MAGEC a la necesaria integración entre producción y mantenimiento sin la cual no podría considerarse eficaz.
El plan de mantenimiento y automantenimiento consiste en las tareas de mantenimiento preventivo, las inspecciones ciclicas, el monitorado, acciones correctivas, normas de comportamiento relativas a la salud y la seguridad, tareas de automanteniemiento y gestión de los repuestos. Además cuenta con una fase de balance de actividades a realizar, que en la práctica se comporta como una ficha de programación donde quedan ubicadas en frecuencia y recuersos y responsabilidad las tareas previamente planificadas. Para todo esto el MAGEC italiano, cuenta con una serie de modelos y fichas a compilar con el propósito de estructurar y garantizar la trazabilidad de todo el proceso de mantenimiento bajo cobertura del MAGEC.
De modo que el MAGEC no es el FMECA. La razón es que el MAGEC partiendo de un análisis FMECA va mucho más allá del análisis de fallos, efectos y criticidad para llegar a la proposición de estructurada de un plan de mantenimiento donde están presentes todas las políticas de mantenimiento (correctiva, preventiva, predictiva, mejorativa) y aspectos relacionados con la organización del trabajo (como el mantenimiento autónomo), junto a criterios logisticos relacionados con la gestión de los repuestos. Todo en un cuerpo organizado y concatenado. Se trata de uno de los caminos para llegar a un plan de mantenimiento. Una alternativa italiana llamada MAGEC por su idea inspiradora, pero al servicio del proceso de mantenimiento durante la fase operativa del ciclo de vida de los activos. n
Para referenciar este documento: Electronic Document: Sexto, Luis Felipe. MAGEC, la versión italiana del FMECA que no es un FMECA. [en línea]. Junio de 2008. [fecha que se cita xx/xx/20xx]. Disponible en Internet: blog Calidad & Mantenimiento <http://luisfelipesexto.blogia.com> . Se permite la reproducción de este documento, siempre que se referencie la fuente y no exista ánimo de lucro
Por Luis Felipe Sexto
EL PROBLEMA DE LAS TECNOLOGÍAS DE MANTENIMIENTO es que no es posible aplicarlas paralelamente a la concepción y cultura que tiene la empresa. Si desde el mantenimiento se exige la interacción con otras áreas de la organización y, a su vez, la empresa trabaja según una cultura mecanicista, entonces no será posible avanzar, debido a la manifiesta incompatibilidad en la forma de entender los procesos de la organización.
El Mantenimiento Centrado en la Confiabilidad (RCM según su sigla en inglés) es una tecnología orientada a la determinación de los requerimientos de mantenimiento de los activos físicos. Aunque su basamento, en esencia, ya estaba planteado en los años 60, no es hasta la década de los 90 que las ideas generales maduraron para la inserción en las industrias convencionales, y han sido ajustadas y extendidas con mayor fuerza por América latina. Aunque, sería totalmente inexacto afirmar que goza de una generalización privilegiada en el grueso de las empresas de los países de mayor desarrollo.
EL RCM trabaja el mantenimiento a nivel de modos de fallos y consecuencias. Este enfoque detallista puede resultar muy útil cuando esta bien orientado; también inútil si divaga y no aprende a discernir lo relevante de lo irrelevante. Tan dañino sería identificar y tratar de establecer tareas para cientos, o miles, de modos de fallos cuyas consecuencias o probabilidad de ocurrencia sea baja o remota; como sólo dar crédito a unos pocos, por subestimar al resto, y no poder evitar las consecuencias de fallos de tipo crítico o catastrófico ―o, quizás, de tipo marginal con alta frecuencia e incontables pérdidas.
No existe impedimento alguno, relacionado con la tecnología misma del RCM, para fusionarse con otras tecnologías aplicadas al manejo del mantenimiento en la empresa. De hecho, haciendo un análisis de puntos comunes, prácticamente todas las tecnologías de mantenimiento se orientan a poder lograr la planificación, ejecución, control y mejora de las funciones que realizan los activos y las personas relacionadas. ¿Dónde está la muralla? El problema, una vez más, queda en el terreno de las ideas y los conceptos de de gestión. Materializado a través de la visión, la actuación y la evolución de la DIRECCIÓN empresarial, que va dejando ver el fruto, a veces exquisito, que llamamos cultura organizacional. ■